-
DavidGood company with nice service and high quality and high reputation. One of our reliable supplier , goods are delivered in time and nice package.
-
John MorrisMaterial experts, rigorous processing, timely discovery of problems in design drawings and communication with us, thoughtful service, reasonable price and good quality, I believe we will have more cooperation.
-
JorgeThank you for your good after-sales service. Excellent expertise and technical support helped me a lot.
-
PetraThrough very good communication all problems solved, satisfied with my purchase
-
Adrian HayterThe goods purchased this time are very satisfied, the quality is very good, and the surface treatment is very good. I believe we will order the next order soon.
50%Mo Molybdenum Tungsten Alloy Plate For High Temperature Parts
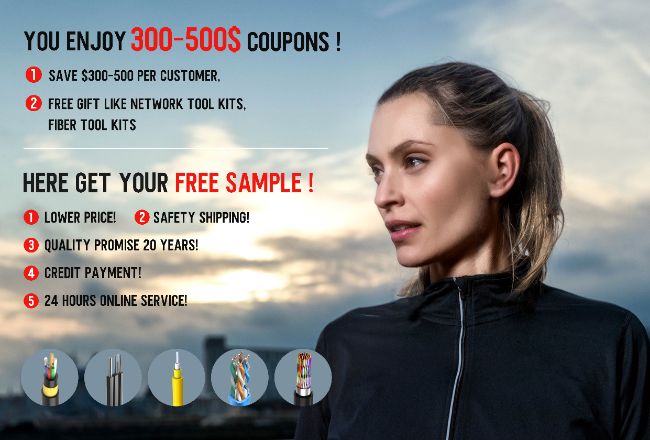
Contact me for free samples and coupons.
Whatsapp:0086 18588475571
Wechat: 0086 18588475571
Skype: sales10@aixton.com
If you have any concern, we provide 24-hour online help.
xName | 50%Mo Molybdenum Tungsten Alloy Plate For High Temperature Parts | Grade | WMo Alloy |
---|---|---|---|
Mo Content | 50%(wt%) | Thickness | 0.3~25mm |
Width | 50~600mm | Length | ≤2500 Mm |
Surface | Polished, Alkaline, Washing Sandblasting | Export Port | Any Port In China |
Standard | ASTM B386 | ||
Highlight | 50%Mo Molybdenum Tungsten Alloy,Molybdenum Tungsten Alloy High Temperature,Molybdenum Tungsten Alloy Plate |
50%Mo Molybdenum Tungsten Alloy Plate For High Temperature Parts
1. Description of 50%Mo Molybdenum Tungsten Alloy Plate For High Temperature Parts:
Molybdenum-tungsten alloy plate is the most commonly produced product among molybdenum-tungsten products. Because molybdenum-tungsten alloy has good high temperature performance, good thermal conductivity, electrical conductivity, low thermal expansion coefficient and high temperature strength, most of them are used in electronic power equipment manufacturing, Metal material processing industry, glass manufacturing, high temperature furnace structural component manufacturing, aerospace and defense industry.
The melting point of molybdenum-tungsten alloy plate increases with the increase of tungsten content. When the tungsten content increases to 25%, the melting point of the alloy is about 200℃ higher than that of pure molybdenum (as shown in the figure below). Therefore, the corresponding alloy composition can be selected in the range of 2620-3410 °C according to the use temperature and the required melting point of the alloy. This advantage is also one of the advantages that molybdenum-tungsten alloys are widely used. The relationship between the content of tungsten in molybdenum-tungsten alloy and the melting point of the alloy is shown in the figure below.
2. Size of 50%Mo Molybdenum Tungsten Alloy Plate For High Temperature Parts:
Thickness :0.3~25mm
Width:50~600mm
Length: ≤2500 mm
Also we can produce as per customer's drawing ,processing various special-shaped parts.
Standard of produce: ASTM B386
3. Hardness of 50%Mo Molybdenum Tungsten Alloy Plate For High Temperature Parts:
The highest room temperature hardness value of molybdenum-tungsten alloy is between 90% and 100% of tungsten content, and its Vickers hardness value is as high as 3530-3860MPa, which is more than double that of pure molybdenum. The highest high temperature hardness value of the alloy is between 70% and 85% tungsten content. When the tungsten content increases from O to 40%, the room temperature tensile strength of the as-processed molybdenum-tungsten alloy increases from 617MPa to 900MPa.
4. Common defects and elimination methods of 50%Mo Molybdenum Tungsten Alloy Plate:
Defects | Causes | Elimination method |
Surface crack | 1) Surface oxide scale and getter layer are not removed 2) The slab thickness is uneven, causing serious uneven deformation 3) The surface cooling is too fast and the plasticity is reduced 4) The heating temperature is uneven and the surface temperature is too low 5) The distribution of the deformation amount of the pass is uneven, and it is suddenly large and small |
1) Strictly control the surface quality 2) The shape of the slab is regular and the size is uniform 3) Used Preheat rolls to prevent the surface of the rolling stock from cooling down too quickly 4) Heating evenly 5) Reasonably distribute the deformation amount of the pass. |
Pit | 1) The heating temperature is too high or the time is too long 2) The scale is peeled off and pressed into the surface |
1) Strictly control the heating temperature and time 2) Control the final rolling temperature to prevent the oxide scale from falling off. |
Surface crater | 1) The burrs on the edge of the board are pressed into the surface of the board 2) The heat-resistant material in the furnace is pressed into the surface when rolling 3) There are foreign objects on the board that are pressed into |
1) Clear the board flash and burr in time 2) Remove foreign matter on the surface of the board in time 3) Timely replacement of rolls |
Scratch | Adhesion or burrs on guide plate, roller table, guide rule, roller | When rolling, pay attention to check the surface and remove the bond in time |
Cracked edge | 1) The slab temperature is uneven and the edge temperature is low 2) Improper configuration of the roll shape and tilting when feeding 3) The deformation of the pass is too large |
1) The heating temperature should be uniform and the operation speed should be fast 2) Adjust the roll shape, and feed it in the correct direction. 3) Control the amount of pass deformation |
Do you want to know more about our products?