-
DavidGood company with nice service and high quality and high reputation. One of our reliable supplier , goods are delivered in time and nice package.
-
John MorrisMaterial experts, rigorous processing, timely discovery of problems in design drawings and communication with us, thoughtful service, reasonable price and good quality, I believe we will have more cooperation.
-
JorgeThank you for your good after-sales service. Excellent expertise and technical support helped me a lot.
-
PetraThrough very good communication all problems solved, satisfied with my purchase
-
Adrian HayterThe goods purchased this time are very satisfied, the quality is very good, and the surface treatment is very good. I believe we will order the next order soon.
WCu10 Tungsten Copper Alloy Spot Welding Electrode Tungsten Copper Rod
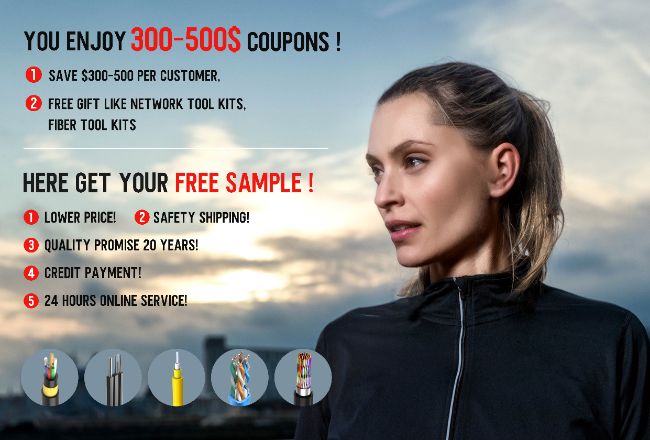
Contact me for free samples and coupons.
Whatsapp:0086 18588475571
Wechat: 0086 18588475571
Skype: sales10@aixton.com
If you have any concern, we provide 24-hour online help.
xName | Tungsten Copper Spot Welding Electrode | Material | Tungsten Copper Alloy |
---|---|---|---|
Grade | WCu10,WCu15,WCu20,WCu25,WCu30 | Characteristic | High Strength, High Specific Gravity |
Surface | Bright | Size | As Per Customer Drawing |
Export Port | Any Port In China | Package | Plywood Case |
Highlight | WCu10 Tungsten Copper Alloy,Welding Tungsten Copper Alloy,WCu15 Tungsten Copper |
Tungsten Copper Spot Welding Electrode
1. The Tungsten Copper Spot Welding Electrode's description:
The tungsten copper alloy is ideal for welding electrodes because it is simple to process, has excellent temperature resistance, arc ablation resistance, a high specific gravity, and good electrical and thermal conductivity.And Tungsten copper spot welding electrode is one of the most critical parts to ensure spot welding quality. Its main functions include directing the current of the spot welder to the workpiece, transferring pressure, and rapidly dissipating heat from the weld zone.
2. Different performance table for different copper content of Tungsten Copper Spot Welding Electrode:
Cu content |
Other impurities | W content |
Density g/cm3 |
Resistance |
Conductivity (%IACS) |
Hardness (HB) | Flexural strength (Mpa) |
50±2 | 0.5 | Remain | 11.85 | 3.2 | 54 | 1128 | / |
45±2 | 0.5 | Remain | 12.30 | 3.5 | 49 | 1226 | / |
40±2 | 0.5 | Remain | 12.75 | 3.7 | 47 | 1373 | / |
35±2 | 0.5 | Remain | 13.30 | 3.9 | 44 | 1520 | / |
30±2 | 0.5 | Remain | 13.80 | 4.1 | 42 | 1716 | 790 |
25±2 | 0.5 | Remain | 14.50 | 4.5 | 38 | 1912 | 885 |
20±2 | 0.5 | Remain | 15.15 | 5.0 | 34 | 2158 | 980 |
15±2 | 0.5 | Remain | 15.90 | 5.7 | 30 | 2354 | 1080 |
10±2 | 0.5 | Remain | 16.75 | 6.5 | 27 | 2550 | 11 |
3. Advantage of Tungsten Copper Spot Welding Electrode:
1. High machining accuracy and small contact area of the tip of the welding tip;
2. The required voltage is low, the welding efficiency is high, and the welding stability is good;
3. It has high enough torsional strength to effectively ensure the quality and precision of processing;
4. The welding quality is high, the welding seam is small, the consistency is good, and the virtual welding is not easy to occur.
4.Common method of Tungsten Copper Spot Welding Electrode:
(1). Special conditions are adopted to increase the influence of heat generation by contact resistance between workpieces and reduce the influence of heat dissipation of electrodes. Capacitor energy storage welding machine can weld workpieces with relatively large thickness by using high current and short power-on time;
(2). Use electrodes with different contact surface diameters to use smaller diameters on the side of thin parts or workpieces with good electrical and thermal conductivity to boost this side's current density and lessen electrode heat dissipation's impact;
(3). Use different electrode material sheets or copper alloys with poor thermal conductivity on one side of the workpiece with good electrical and thermal conductivity to reduce heat loss on this side;
(4). Use a process gasket to pad a gasket made of metal with poor thermal conductivity (thickness is 0.2-0.3mm) on the side of the thin piece or the workpiece with good electrical and thermal conductivity to reduce heat dissipation on this side.
