-
DavidGood company with nice service and high quality and high reputation. One of our reliable supplier , goods are delivered in time and nice package.
-
John MorrisMaterial experts, rigorous processing, timely discovery of problems in design drawings and communication with us, thoughtful service, reasonable price and good quality, I believe we will have more cooperation.
-
JorgeThank you for your good after-sales service. Excellent expertise and technical support helped me a lot.
-
PetraThrough very good communication all problems solved, satisfied with my purchase
-
Adrian HayterThe goods purchased this time are very satisfied, the quality is very good, and the surface treatment is very good. I believe we will order the next order soon.
Alkaline Washing Material TZM Molybdenum Alloy Tray Tzm Metal Alloy Boats welding boat riveting boat
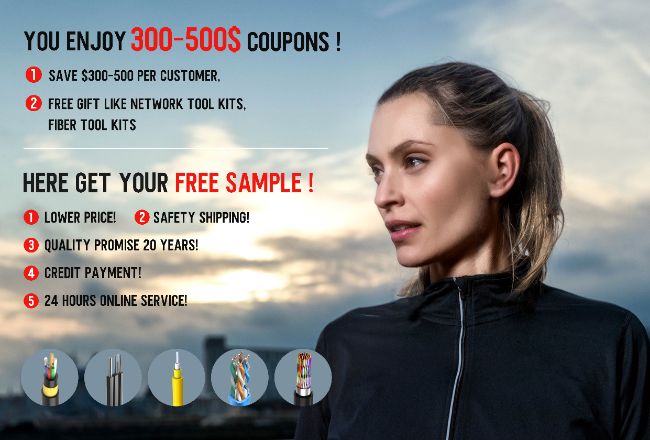
Contact me for free samples and coupons.
Whatsapp:0086 18588475571
Wechat: 0086 18588475571
Skype: sales10@aixton.com
If you have any concern, we provide 24-hour online help.
xName | TZM Molybdenum Alloy Tray | Material | Titanium Zirconium Molybdenum Alloy |
---|---|---|---|
Grade | TZM | Shape | Tray |
Size | As Per Customer's Drawing | Surface | Bright,Alkaline Washing |
Craft | Riveted,Sintering,Welding,Stamping | MOQ | 1pc |
Highlight | Alkaline Washing TZM Molybdenum Alloy,TZM Molybdenum Alloy Tray,Material TZM |
TZM Molybdenum Alloy Tray
1. Description Of TZM Molybdenum Alloy Tray:
TZM alloy has high temperature resistance, high strength, high melting point, high elastic modulus, small linear expansion coefficient, strong corrosion resistance and good electrical and thermal conductivity, so it is widely used in various applications. TZM alloys are also often prepared into tray for the production of molybdenum powder. Molybdenum powder should be produced in a high temperature environment above 1000°C. The boat containing molybdenum powder should be resistant to high temperature and not easily deformed, and no oxidation reaction will occur at high temperature, resulting in impurities and reducing the purity of molybdenum powder. The TZM alloy not only meets the above requirements, but also the strength of the molybdenum powder prepared by the alloy is improved to a certain extent, and the impurity composition of the molybdenum powder is not increased. Titanium-zirconium-molybdenum alloys are made into boats, usually by a combination of stamping and welding.
2. Size Of TZM Molybdenum Alloy Tray:
TZM tray generally include riveted tray, welding tray, folding tray, and stamping boats. Generally, there is no fixed size, and they are all customized according to the customer's drawing requirements.
3. Performance Of TZM Molybdenum Alloy Tray:
Material | Density /g·cm-3 | Melting point/℃ | Boiling point/℃ |
TZM alloy(Ti0.5/Zr0.1) | 10.22 | 2617 | 4612 |
Mo | 10.29 | 2610 | 5560 |
Mechanical properties |
Elongation /% |
Elastic Modulus /GPa |
Yield Strength /MPa |
Tensile strength /MPa |
Fracture toughness/(MP·m1/2) |
Data | ≤20 | 320 | 560-1150 | 685 | 5.8-29.6 |
4. Production Steps Of TZM Molybdenum Alloy Tray:
1). Obtain the TZM alloy plate by vacuum furnace smelting method or powder metallurgy method, in which the forming temperature of the alloy boat is 600 ℃, and the heating method is isothermal forming, that is, a thermal resistance is set in the mold, and the blank holder is selected with low thermal conductivity. materials to reduce the heat transfer between the plate and the air, so that during the heating process, the temperature of the alloy and the mold can be balanced as much as possible at 600 °C;
2). Select tungsten argon arc welding (TIG) welding process to weld TZM alloy, when the welding current is 210A, the welding speed is 4mm/s, and the argon gas flow is 8-12L/min, the alloy weld is the best;
3). Since the TZM alloy will oxidize at high temperature, it is necessary to carry out anti-oxidation treatment when processing the alloy. At 0~400℃, the oxidation rate of the alloy is slow, and volatilized MoO2 will be formed on the surface. At 400~750℃, the alloy will be rapidly oxidized, and volatile MoO3 will be formed on the surface. At 800-10000°C, the alloy quality decreases significantly, which is caused by the evaporation of MnO3.
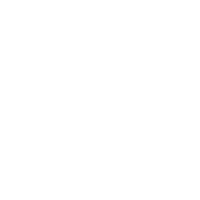
Do you want to know more about our products?